Los musculitos el plástico
¿Combustible o materia prima? Nuestro socio ELM de Bissingen ha combinado ambas formas de reciclar y, como resultado, ha conseguido esto...
Incluso la botella de agua de la sala de conferencias del Grupo ELM en su sede de Bissingen está etiquetada en negrita: "Reciclaje", y en la etiqueta también se representa un ciclo. En el caso de la botella de agua, ahora sabemos que al final volverá al circuito de reciclaje. Esto es igual que con otros productos de plástico que ELM ha sabido reciclar. Hoy descubrimos más durante una visita a la fábrica de Matthias Einsele, que comparte la dirección y las acciones de la empresa al 50:50 con Eberhard Lebküchner. Es capaz de describir su negocio de forma tan detallada como probablemente sólo puede hacerlo alguien que separa plásticos en granulometrías y fracciones específicas por vocación.
Para empezar: ELM es uno de nuestros socios y proveedor de plástico reciclado de alta calidad, que utilizamos para fabricar depósitos de agua de lluvia en Teningen, Herbolzheim, Neuried y Dachstein. ELM, fundada en 1998 por Einsele, Lebküchner y Willi Männer en Bissingen an der Teck, en el distrito de Esslingen (Baden-Wurtemberg), ahora es un grupo de empresas con más de 200 empleados y nueve empresas en cinco localizaciones. Los dos eslóganes "De residuo a recurso" y "De residuo a combustible" describen acertadamente la línea estratégicaque ELM sigue con la materia prima plástica. Todo empezó con el combustible ...
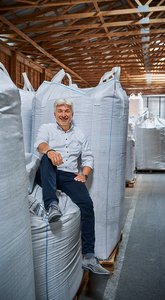
Combustibles derivados de residuos (CDR)
El Sr. Männer, que anteriormente había gestionado un servicio de contenedores, inició la fusión de varias empresas regionales de gestión de residuos y asumió el cargo de director gerente de la planta que luego adquirieron las empresas de gestión de residuos. Al mismo tiempo, quedó vacante un almacén textil en Bissingen. Y los tres fundadores de Bissingen materializaron aquí su idea: "La planta de clasificación de la empresa de gestión de residuos permitía separar los materiales entregados de tal forma que pudiéramos seguir trabajando con ellos", recuerda Einsele. "Nos interesaba el plástico y, en particular, los compuestos plásticos que no se podían reciclar". La empresa recién fundada los convirtió en combustibles. Las piezas de plástico se separan de los residuos y se moldean de forma que sean fácilmente inflamables y ardan según sus propiedades, liberando la mayor cantidad de energía posible. Los residuos de alto valor calorífico contienen mucha energía. "Esta energía debe utilizarse de forma razonable", coinciden Einsele, Lebküchner y Männer. En el sentido más sostenible.
El alto nivel energético caracteriza al RDF
Pueden sustituir al gas y al carbón como combustibles. Desempeñan un papel central en las caleras, las centrales térmicas de carbón y la producción de cemento, donde se requieren altas temperaturas en todas partes. En ELM, el combustible se destina exclusivamente a las cementeras. El plástico arde en enormes hornos rotatorios de seis metros de diámetro y garantiza la producción de gruesos ladrillos de clínker en la parte inferior como precursor del cemento posterior. No se depositan residuos de plástico en los ladrillos porque la naturaleza bidimensional del plástico hace que se queme completamente antes. En otras palabras, las piezas de plástico se aplastan por completo. "En su entorno específico, se queman con menos contaminantes que el polvo de carbón al que sustituyen", subraya Einsele. Sin duda, mejoran la huella de carbono de la producción de cemento.
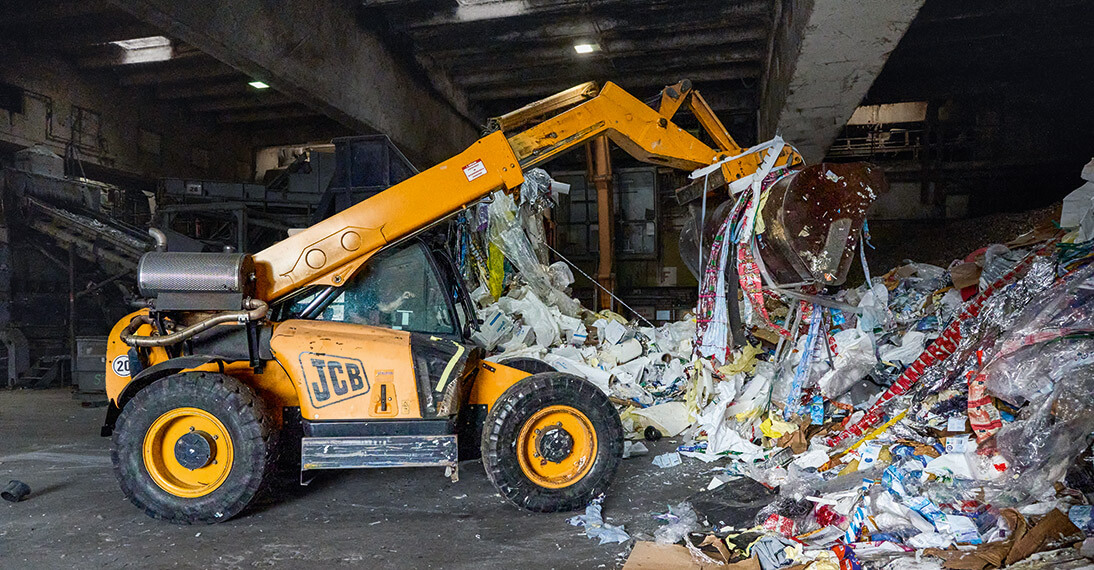
"Es pura ironía que las incineradoras de residuos alemanas sigan sin pagar un impuesto sobre el CO2, pero las cementeras tengan que hacerlo en toda Europa, aunque sustituyan el carbón pulverizado por CDR", afirma Einsele, buen conocedor de la producción de cemento. Tanto es así que ELM ha construido sus plantas de Mergelstetten, Allmendingen y Harburg justo al lado de las cementeras que allí se encuentran. "Con las grandes cantidades que suministramos a nuestros clientes a largo plazo y adaptadas a la producción respectiva, sólo tiene sentido de esta manera", dice Einsele. "En 1998 dijimos que si podíamos producir 12.000 toneladas de RDF al año, seríamos felices. Ahora son casi 300.000 toneladas al año".
En 2011, ELM cerró el ciclo y abrió la segunda vía
De residuo a recurso, a materia prima. La palabra mágica es reciclaje de materiales. Gracias a la mejora de los procesos, ELM ahora podía separar los plásticos de sus CDR en fracciones cada vez más finas. Al mismo tiempo, esto tenía la ventaja de hacer que el RDF fuera más reactivo, es decir, más fácil de encender. Por ello, en 2017, ELM recibió el certificado avalando que es una de las 100 empresas más eficientes en el uso de recursos de Baden-Württemberg por la Elevada tasa (hasta el 100% ) de sus CDR en el quemador de la planta de cemento.
Gracias a la nueva separación de materiales, ahora sobraban las piezas más grandes de plástico duro
¿Qué hacer con ellas? Con nuestra pregunta, ELM encontró una respuesta clara: ¡volver al ciclo! Estamosencantados, ya que estamos constantemente en busca de nuevas fuentes de materias primas. ELM ha adaptado en consecuencia su sistema de separación a nuestras necesidades y así promovimos la nueva rama del grupo de empresas ELM: "En colaboración con GRAF, hemos configurado nuestro sistema de separación de tal manera que las poliolefinas, también conocidas como PO, que son valiosas para GRAF, se separan de forma fiable". Las piezas de plástico pretrituradas se separan en una especie de piscina con tecnología de sumidero flotante, explica Einsele más adelante. A continuación se realiza la limpieza posterior, que incluye la eliminación de las fibras mezcladas, y finalmente el envasado de los copos de PO acabados en grandes sacos. En el pabellón 2, que Einsele nos muestra ahora, además de los big bags habituales para la entrega, se utiliza ahora un semirremolque de camión con una capacidad de más de 90 metros cúbicos.
"GRAF es uno de los pocos fabricantes que está plenamente comprometido con la sustitución de plásticos primarios por reciclados. Incluso en el punto álgido de la pandemia, GRAF siguió haciéndonos pedidos, y ahora hemos suministrado a GRAF un total de más de 16.000 toneladas de copos de PO. En la actualidad, los plásticos primarios son demasiado baratos, y precisamente por eso asociaciones como la que mantenemos con GRAF son tan cruciales".
ELM seguirá creciendo en reciclaje a medio y largo plazo
"En el sector de los CDR, ya casi hemos cubierto el consumo de combustible de nuestros clientes. El camino 'de residuo a recurso' no es sólo una cuestión de convicción para nosotros, sino también de ventas", afirma Einsele. Por cierto, también se utiliza la espectroscopia de infrarrojo cercano (NIR) para separar los valiosos plásticos reciclados. Es la misma tecnología que posteriormente separa las poliolefinas en PE y PP.