Bauer sucht Plastik
Landwirt, Tüftler, Saubermacher: Bernhard Wilken ist so vielseitig wie sein Emsländer Unternehmen. Und das ist nicht nur Hühnerhof, sondern auch ein wichtiger Teil unseres GRAF Recycling-Kreislaufs. Erfahren Sie im nachfolgenden Bericht, welche Maßnahmen die Firma Wilken im Bereich Nachhaltigkeit bereits unternimmt und wie sie mit uns zusammenarbeiten:
Wenn es eine Sache gibt, die den Chef auf die Palme bringt, dann ist das Energieverschwendung. „Oh, das mag Herr Wilken gar nicht!“, bestätigt uns ein Mitarbeiter hinter vorgehaltener Hand. Doch er habe ja recht: „Alle Welt redet von Nachhaltigkeit, für uns gehören geschlossene Kreisläufe hingegen schon immer dazu“, fügt er hinzu. Und so wird auf dem Familienhof in Haren eben nicht nur die hofeigene Biogasanlage zur eigenen Energieerzeugung genutzt, sondern auch die Restwärme daraus für den Hühnerstall und zum Trocknen von gewaschenem Kunststoff verwendet – der dann später wiederum recycelt wird. Und das Federvieh kriegt auch nicht irgendwas zum Picken, sondern Bio-Futter vom eigenen Feld – während der Dung dann wiederum in der Biogasanlage landet. Kreislauf à la Wilken. Wie das jetzt mit der Landwirtschaft und dem Plastik genau zusammenhängt? Am besten, wir fangen mit der Geschichte mal von vorne an …
Die Geschichte der Firma Wilken
Wir sind im Emsland, nur einen Steinwurf von der niederländischen Grenze entfernt. Auf einem Stück Land, das auf den ersten Blick mit seinem saftigen Grün nicht nur liebenswürdig, sondern auch unwahrscheinlich weit erscheint. Norddeutschland eben. Der Sommerweizen raschelt vor dem Hof der Wilkens im Wind. Von Westen ziehen Wolken auf, die Regen versprechen, aber dann doch keinen bringen. „Schade“, meint Bernhard Wilken dazu, während er uns später über seinen Hof führt. „Den könnten wir eigentlich gut gebrauchen, damit hier auch alles so schön grün bleibt.“ Die Hofpferde haben sich trotzdem lieber vorsorglich in ihren Stall verzogen.
Seit 1931 steht hier der Familienhof, den Opa Wilken einst gegründet hatte. Bernhards Vater hatte die Landwirtschaft im Haupterwerb fortgeführt. Der Sohnemann allerdings, immer schon technikbegeistert, hat sich dann für eine Ausbildung zum Landwirt, den Nebenerwerb und eine zusätzliche Lehre zum Konstruktionsmechaniker entschieden. Ein Glück, wenn man im Nachhinein betrachtet, was aus dem Hof, auf dem mit Sohn Henrik bereits die nächste Wilken-Generation mit anpackt, als Keimzelle der Wilken-Gruppe geworden ist. Denn Bernhard Wilkens Fingerfertigkeit und sein Verständnis für Maschinen und Mechanik haben den Familienbetrieb kräftig wachsen lassen.
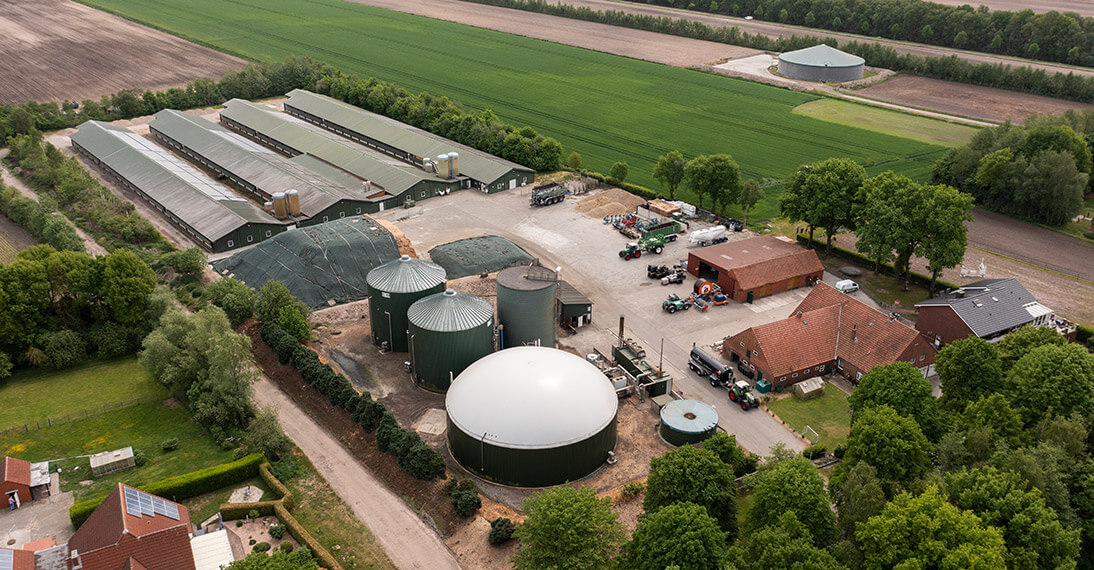
65 Mitarbeiter beschäftigt er inzwischen. Davon kümmern sich 45 bei Wilken Plastics Energy darum, dass angelieferte Kunststoffabfälle geschreddert, gewaschen und sortiert werden. Von hier aus geht ein großer Teil der Kunststoffabfälle schließlich in unser Kompetenzzentrum Rohstoffe nach Herbolzheim, wo es zu Rezyklaten weiterverarbeitet und wiederverwertet wird – für langlebige Lösungen rund um das wichtige Thema Regenwassermanagement. So wird Nachhaltigkeit noch ein Stück weiter gedacht – bis hin zum fertigen Produkt.
Schreddern, waschen, trocknen
„Im Prinzip sind die Vorgänge beim Plastikwaschen die gleichen wie in der Futtermittelherstellung“, antwortet Wilken auf die sich aufdrängende Frage, wie man denn überhaupt auf so eine Idee kommt. Und zwar so nüchtern, wie sie eben sind, die Menschen aus dieser besonderen Region, die aufgrund ihrer Abgeschiedenheit irgendwie schon immer auf gute Ideen angewiesen waren. „Für mich lag das auf der Hand, und außerdem hat mich damals geärgert, dass wir die Restwärme unserer Biogasanlage nur im Winter zum Heizen der Hühnerställe nutzen konnten“, erzählt der Unternehmer.
Im Sommer sei sie dann einfach verpufft. Inzwischen leitet ein sechs Kilometer langes Rohr das Biogas unter den Feldern der Familie in ein Blockheizkraftwerk bei der Wasch- und Sortieranlage, die Bernhard Wilken vor gut 15 Jahren selbst geplant und entwickelt hat. Dort wird das Gas zu Biostrom und Biowärme umgewandelt. „Bei uns wird nichts mehr verschwendet. Alles hängt zusammen“, sagt Wilken. Mit gut sechs Millionen Kilowattstunden Strom bleibt sogar noch was über für benachbarte Bauern.
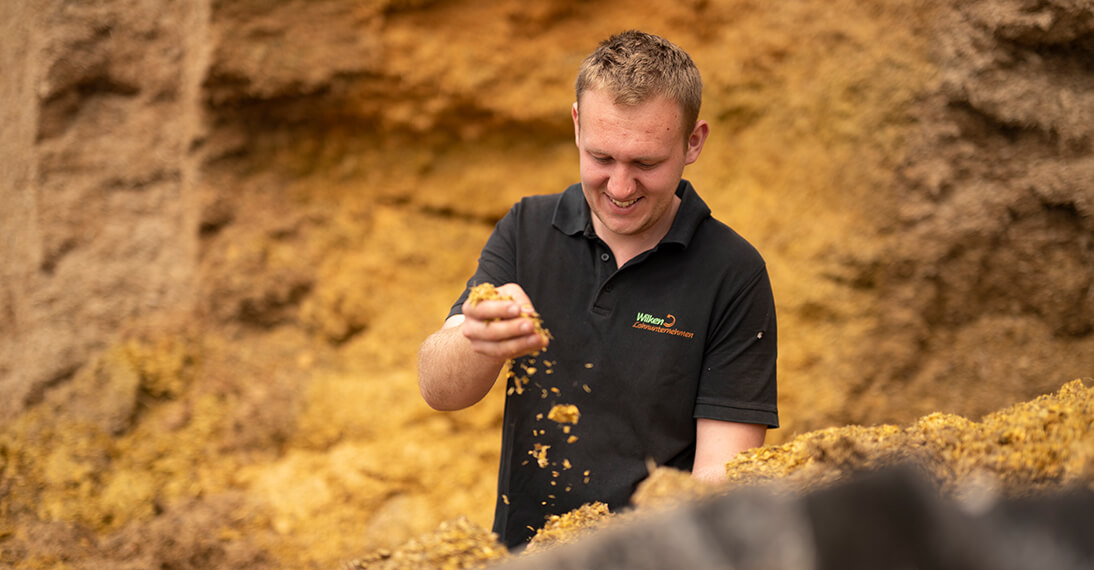
Wilkens Beitrag zum Klimaschutz
Das Familienunternehmen produziert die selbst benötigte Energie komplett autark. Und obendrein leistet das Unternehmen dabei auch noch einen erheblichen Beitrag zum Klimaschutz: Das Verfahren spart den CO2-Verbrauch von 1300 Pkw im Jahr ein. „Das sind die Zusammenhänge, wie wir sie in diesen Zeiten alle wieder verstärkt in den Blick fassen sollten“, findet der Chef. „In der Natur wird ja auch nichts verschwendet.“
Wir fahren mit Bernhard Wilken rüber in die Plastikverarbeitung. Im E-Audi, klar, wenn man zu Hause eigenen Strom hat. Sechs Kilometer ab Hof, direkt an der Autobahn gelegen, erkennen wir das Wilken-Logo schließlich an der Pforte wieder. Auf dem Hof wird gerade ein Lkw mit frisch gewaschenem, geschreddertem Kunststoff bestückt. 25 Tonnen passen hinein. Vier solcher Trucks verlassen fast jeden Tag das Werksgelände. Im Jahr kommen so 35 000 Tonnen Recyclingmaterial zusammen, die bei Wilken Plastics aufbereitet werden. Apropos aufbereitet: Das geschieht auch mit dem Wasser, das zum Waschen des Kunststoffs verwendet wird. Dabei wird die schmutzige Flüssigkeit durch ein spezielles Filtersystem geleitet, aufgefangen und geklärt. Ein Kreislauf, was sonst!
»Bei uns wird nichts verschwendet, alles hängt zusammen. So schaffen wir es, die Kunststoffe möglichst nachhaltig zu reinigen«
Rund um die alte Werkhalle türmt sich meterhoch der angelieferte Plastikmüll – bereit zum Zerkleinern, Waschen und Sortieren. Lange liegt er hier allerdings nicht herum. Aus der Halle dröhnt es entsprechend. Die Maschinen laufen unter Volllast. Zu tun gibt es schließlich genug. Die Nachfrage nach dem aufbereiteten und vorsortierten Recyclingmaterial ist riesig. Gleich nebenan baut Bernhard Wilken deshalb bereits eine neue, noch größere Anlage mit noch kraftvolleren und effizienteren Maschinen. Viele Ideen dafür stammen wieder vom Chef selbst. 10 Millionen Euro nimmt er dafür in die Hand. In Nachhaltigkeit zu investieren, sei vor 15 Jahren schon richtig gewesen – und jetzt umso richtiger, meint der Emsländer Tüftler.
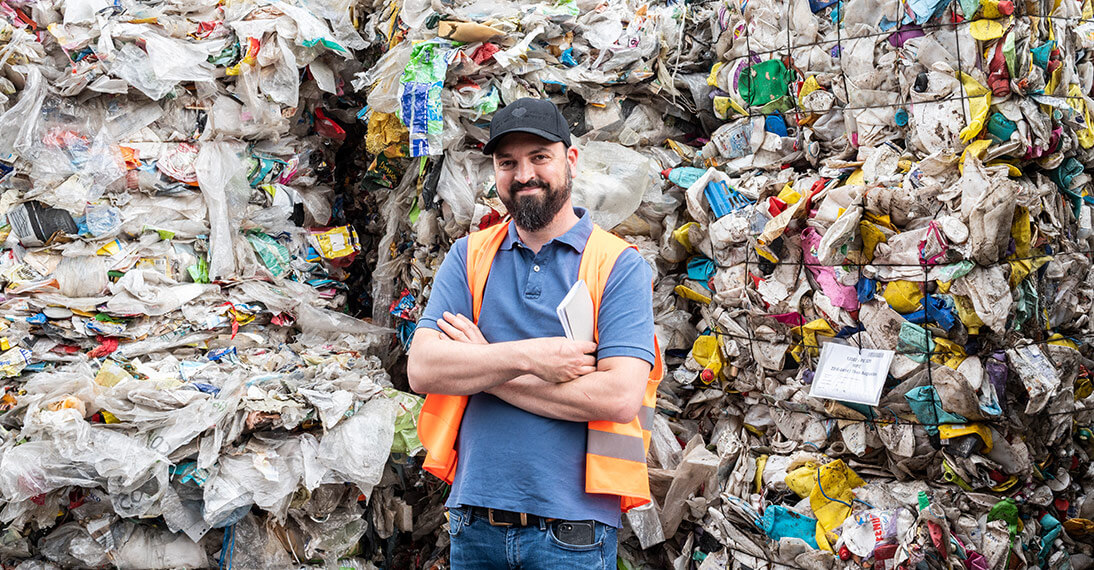
Der Radlader kippt quasi im Minutentakt die Kunststoffabfälle in einen Trichter. Anschließend geht er in die Sortieranlagen, die Bernhard Wilken zu großen Teilen mitentwickelt hat, wo die Kunststoffe vorsortiert werden. Wie die Maschinen im Detail funktionieren? „Das bleibt natürlich unser Betriebsgeheimnis“, sagt Bernhard Wilken schmallippig und grinst verschmitzt. Irgendwas mit Kreislauf. So viel haben wir auf jeden Fall verstanden…